APPLICATION DEVELOPMENT CENTER
An ADC plays a crucial role in driving innovation, ensuring that products are optimized for their intended applications, and maintaining a competitive edge in the market.
Charpy/Izod Impact
Test
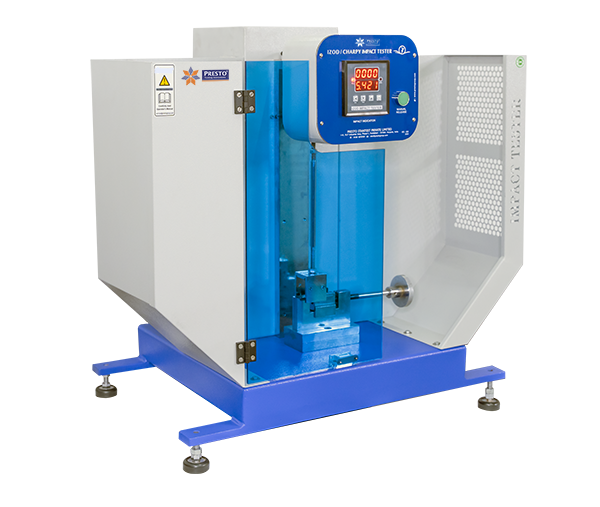
- Purpose: Measures the impact strength of materials by assessing their ability to absorb energy during fracture.
- Sample Preparation: Requires samples to be notched and placed in the impact testing machine.
- Test Method: A pendulum strikes the notched sample, and the energy absorbed is measured.
- Applications: Used in automotive, aerospace, and packaging industries to ensure material durability.
- Data Analysis: Provides insight into material toughness and brittleness.
- Standard Compliance: Tests are conducted according to ASTM and ISO standards.
- Equipment: Utilizes high-precision pendulum impact testers.
- Reporting: Results include energy absorption values, indicating the material’s impact resistance.
MELT FLOW INDEX
(MFI)
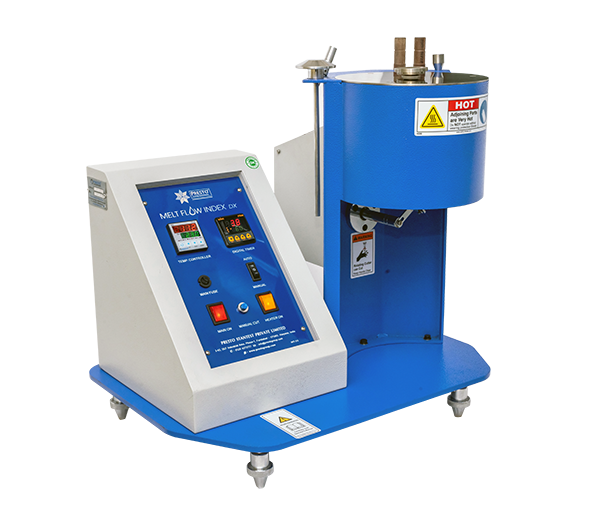
- Purpose: Determines the flow rate of melted polymer to evaluate its processability.
- Sample Preparation: Polymer pellets are loaded into a heated barrel.
- Test Method: Melted polymer is extruded through a die under a specified weight.
- Applications: Crucial for plastic manufacturing processes like injection molding and extrusion.
- Data Analysis: Measures the amount of polymer extruded in a given time, indicating viscosity.
- Standard Compliance: Conducted according to ASTM D1238 and ISO 1133.
- Equipment: Requires a melt flow indexer with controlled temperature settings.
- Reporting: Results are expressed in grams per 10 minutes, providing flow rate data.
COLOR MATCHING
BOOTH
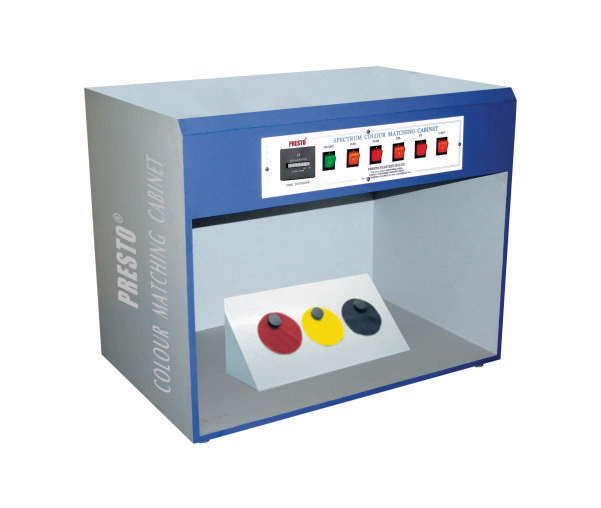
- Purpose: Ensures accurate color consistency and quality in polymer products.
- Sample Preparation: Samples are prepared and placed in the booth under controlled lighting.
- Test Method: Visual inspection of samples under standardized lighting conditions.
- Applications: Used in industries where precise color matching is critical, such as automotive and consumer goods.
- Data Analysis: Compares samples to standard color references.
- Standard Compliance: Adheres to ASTM D1729 and ISO 3668 standards.
- Equipment: Utilizes color matching booths with multiple light sources.
- Reporting: Results include visual assessments and color difference measurements.
NOTCH CUTTER
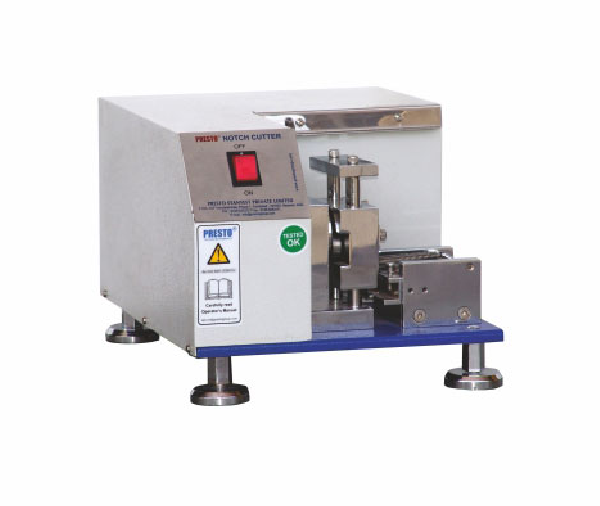
- Purpose: Prepares samples with notches for impact testing.
- Sample Preparation: Polymer samples are precisely notched using the cutter.
- Test Method: Ensures consistent notch depth and shape for accurate impact testing.
- Applications: Used in conjunction with impact tests like Charpy and Izod.
- Data Analysis: Accurate notch preparation is crucial for reliable impact test results.
- Standard Compliance: Follows ASTM D256 and ISO 179 standards.
- Equipment: Employs high-precision notch cutters.
- Reporting: Provides details on notch dimensions and sample preparation.
SPECTRO PHOTO
METER
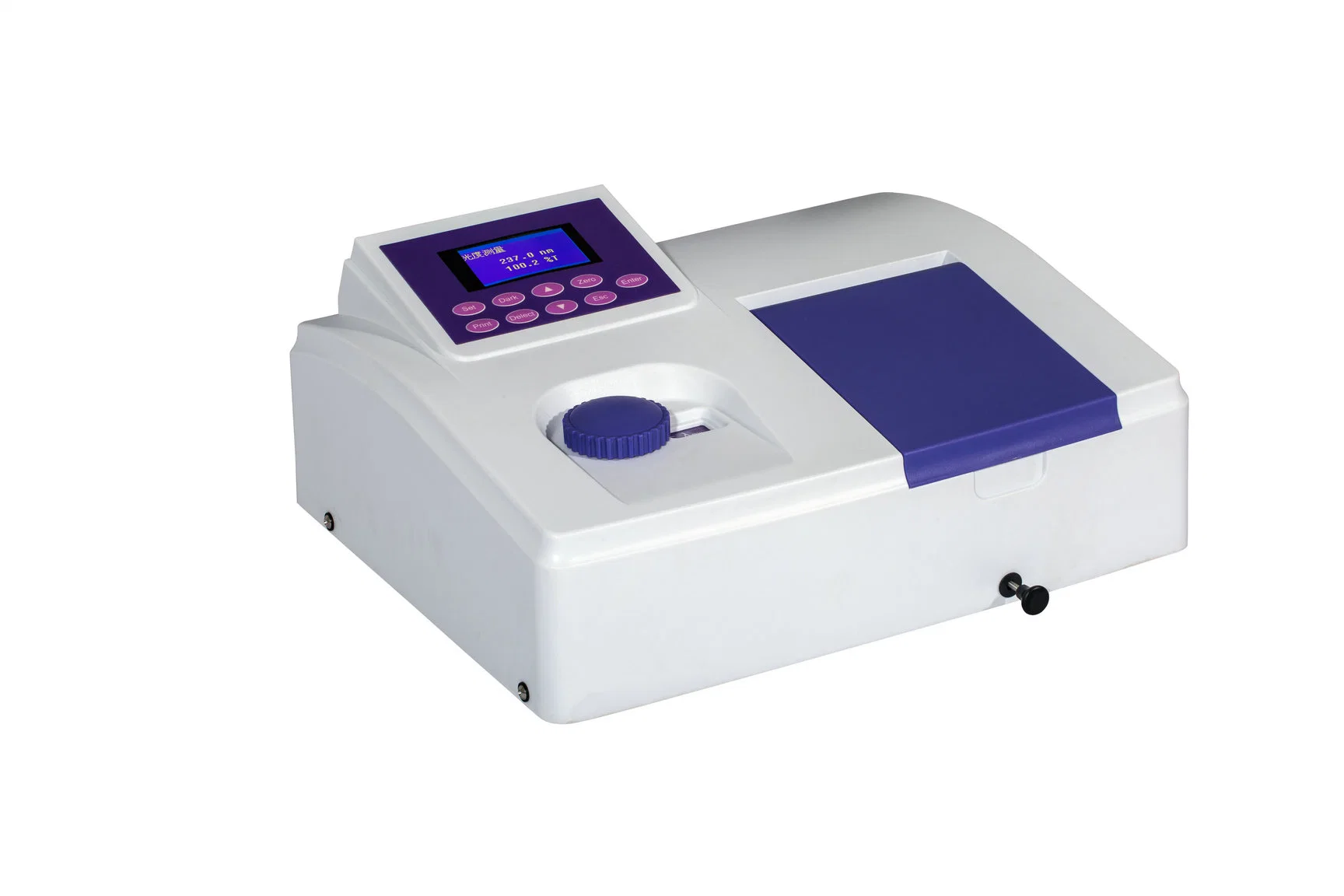
- Purpose: Analyzes the color and quality of polymer materials.
- Sample Preparation: Samples are cleaned and placed in the spectrophotometer.
- Test Method: Measures the absorbance and reflectance of light by the sample.
- Applications: Used for quality control in various industries to ensure color accuracy.
- Data Analysis: Provides detailed color metrics like Lab* values.
- Standard Compliance: Conducted according to ASTM E308 and ISO 7724.
- Equipment: Utilizes advanced spectrophotometers with high accuracy.
- Reporting: Results include comprehensive color data and comparisons to standards.
UNIVERSAL TESTING
MACHINE (UTM)
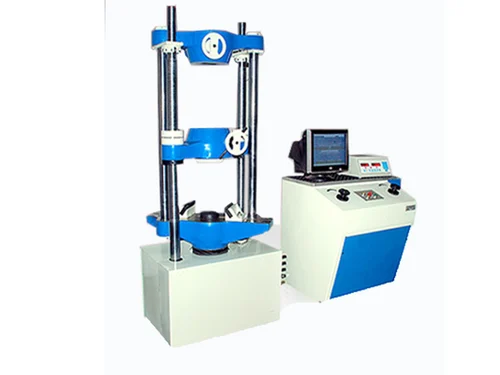
- Purpose: Performs tensile, compression, and bending tests on polymer samples.
- Sample Preparation: Samples are prepared according to the specific test requirements.
- Test Method: Applies controlled force to the sample and measures its response.
- Applications: Used to determine mechanical properties like strength, elasticity, and deformation.
- Data Analysis: Provides stress-strain curves and material property data.
- Standard Compliance: Adheres to ASTM D638 and ISO 527 standards.
- Equipment: Uses versatile universal testing machines with various attachments.
- Reporting: Results include detailed mechanical property measurements.
MUFFLE FURNACE
(FILLER TEST)
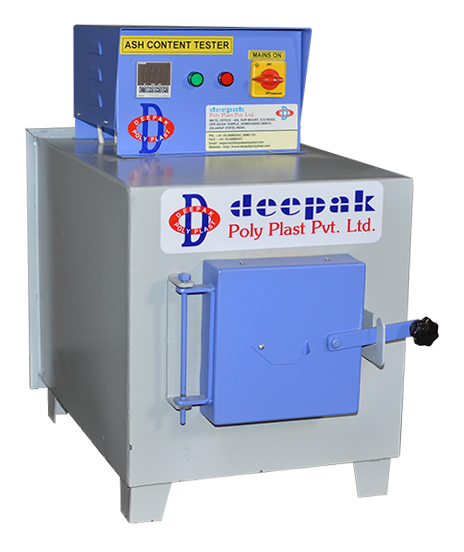
- Purpose: Determines filler content in polymer samples.
- Sample Preparation: Samples are weighed and placed in the furnace.
- Test Method: Samples are heated to a high temperature to burn off the polymer matrix.
- Applications: Used in material composition analysis to quantify filler content.
- Data Analysis: The weight of the residue indicates the filler content.
- Standard Compliance: Conducted according to ASTM D5630 and ISO 3451.
- Equipment: Utilizes high-temperature muffle furnaces.
- Reporting: Results include percentage of filler content in the sample.
DRYING OVEN

- Purpose: Removes moisture from polymer samples before testing.
- Sample Preparation: Samples are cleaned and placed in the drying oven.
- Test Method: Samples are heated at controlled temperatures to eliminate moisture.
- Applications: Essential for accurate testing of moisture-sensitive materials.
- Data Analysis: Ensures samples are free of moisture for reliable test results.
- Standard Compliance: Follows ASTM D618 and ISO 291 standards.
- Equipment: Uses precision drying ovens with temperature control.
- Reporting: Results confirm moisture content has been effectively removed.
MOISTURE ANALYZER
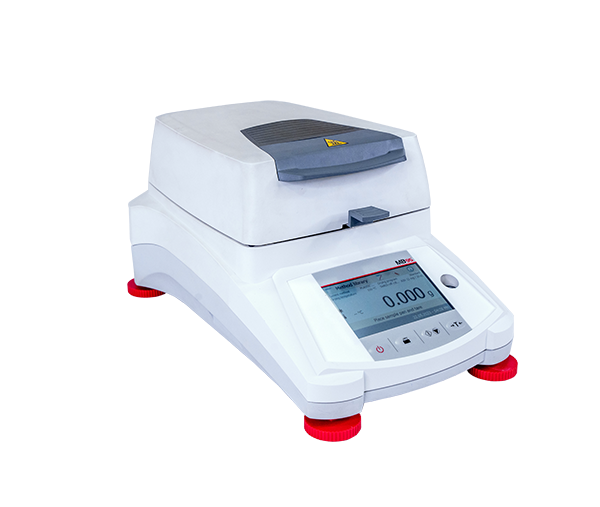
- Purpose: Measures moisture content in polymer samples.
- Sample Preparation: Samples are weighed and placed in the moisture analyzer.
- Test Method: Uses heat and weight loss measurement to determine moisture content.
- Applications: Critical for quality control in polymer production.
- Data Analysis: Provides precise moisture content values.
- Standard Compliance: Adheres to ASTM D6980 and ISO 15512 standards.
- Equipment: Utilizes advanced moisture analyzers with high accuracy.
- Reporting: Results include moisture content percentage.
GLOW WIRE TEST
INSTRUMENT
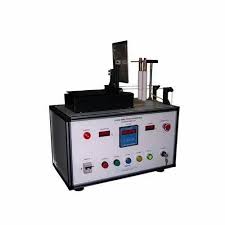
- Purpose: Assesses fire resistance of polymer materials.
- Sample Preparation: Samples are prepared and placed in the testing apparatus.
- Test Method: Applies a heated wire to the sample to evaluate its flammability.
- Applications: Used for safety testing in electrical and electronic industries.
- Data Analysis: Measures the time and behavior of material combustion.
- Standard Compliance: Conducted according to IEC 60695-2-10.
- Equipment: Uses specialized glow wire testing instruments.
- Reporting: Results include ignition time and material behavior under heat.
UL 94 FLAMMABILITY
TEST INSTRUMENT
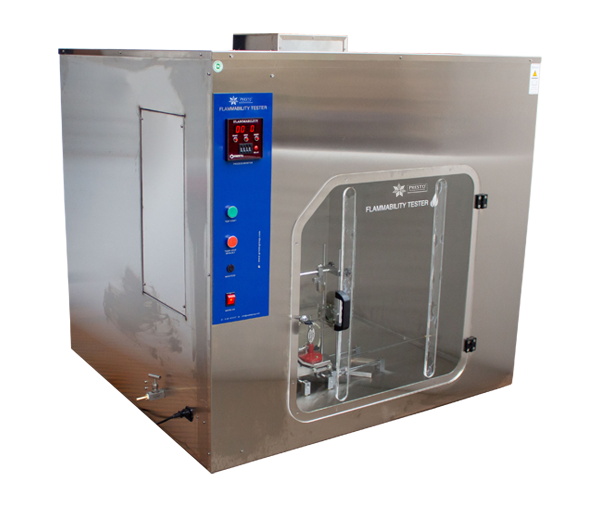
- Purpose: Evaluates the flammability characteristics of polymer materials.
- Sample Preparation: Samples are cut to specified dimensions and conditioned.
- Test Method: Samples are exposed to a flame and observed for burning behavior.
- Applications: Used for material safety and regulatory compliance.
- Data Analysis: Classifies materials based on their burning rate and self-extinguishing properties.
- Standard Compliance: Adheres to UL 94 standards.
- Equipment: Utilizes flammability test instruments with controlled flame sources.
- Reporting: Results include material classification and burning behavior data.
DENSITY TESTER
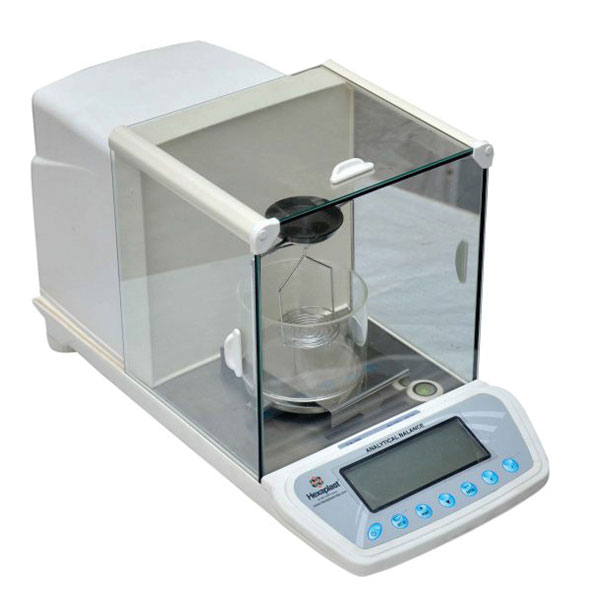
- Purpose: Determines the density of polymer samples.
- Sample Preparation: Samples are weighed and measured.
- Test Method: Uses displacement or flotation methods to measure density.
- Applications: Important for material identification and quality control.
- Data Analysis: Provides precise density values for material comparison.
- Standard Compliance: Conducted according to ASTM D792 and ISO 1183.
- Equipment: Uses density testing equipment with high accuracy.
- Reporting: Results include density measurements and material identification.
WEATHER TEST
EQUIPMENTS
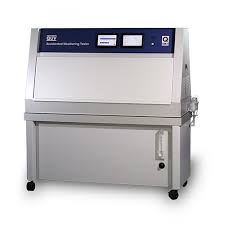
- Purpose: Simulates environmental conditions to test material durability.
- Sample Preparation: Samples are placed in the weather testing chamber.
- Test Method: Exposes samples to cycles of UV light, temperature, and humidity.
- Applications: Used to evaluate material performance in outdoor environments.
- Data Analysis: Assesses changes in material properties over time.
- Standard Compliance: Adheres to ASTM G154 and ISO 4892 standards.
- Equipment: Utilizes weather test chambers with controlled environmental conditions.
- Reporting: Results include material degradation and performance data.
VOLUME / SURFACE
RESISTIVITY
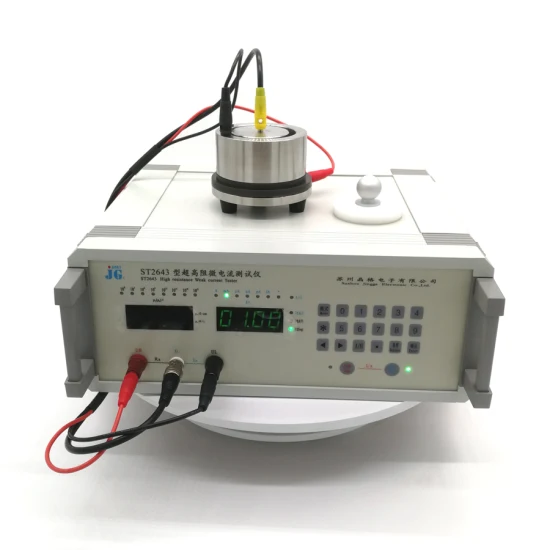
- Purpose: Measures the electrical resistance of polymer materials.
- Sample Preparation: Samples are cleaned and placed in the testing apparatus.
- Test Method: Applies a voltage and measures the resulting current.
- Applications: Critical for materials used in electrical and electronic applications.
- Data Analysis: Provides resistivity values for material classification.
- Standard Compliance: Conducted according to ASTM D257 and IEC 60093 standards.
- Equipment: Uses specialized resistivity testing instruments.
- Reporting: Results include volume and surface resistivity measurements.
HEAT DEFLECTION
TEMPERATURE
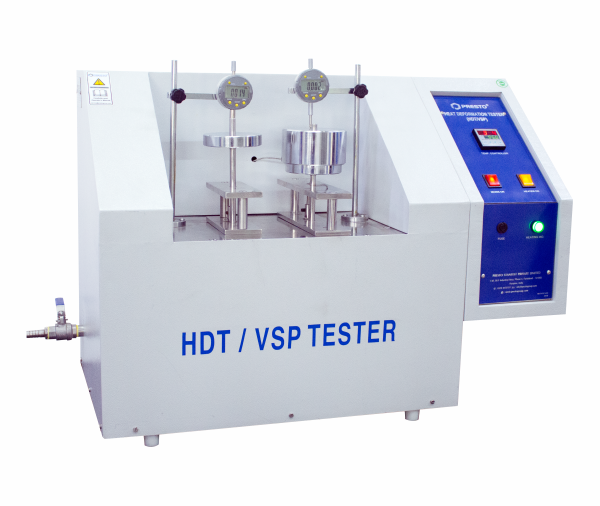
Heat Deflection Temperature (HDT) is the temperature at which a polymer begins to deform under a specified load, indicating its thermal performance.
- Purpose: Measures a material’s resistance to deformation at high temperatures.
- Sample Preparation: Clean samples are mounted in a testing apparatus.
- Test Method: A load is applied, and the temperature is gradually increased until the material deflects.
- Applications: Important for materials used in high-temperature environments like automotive and electronics.
- Data Analysis: Provides the HDT value, indicating thermal stability.
- Standard Compliance: Conducted per ASTM D648 or ISO 75 standards.
- Equipment: Requires specialized testing instruments.
- Reporting: Results include the HDT value, critical for material selection.